2025.3.26-3.29Shenzhen World Exhibition & Convention Center
This is the third exhibition we visited in the past month and stands out as the largest among the three events.
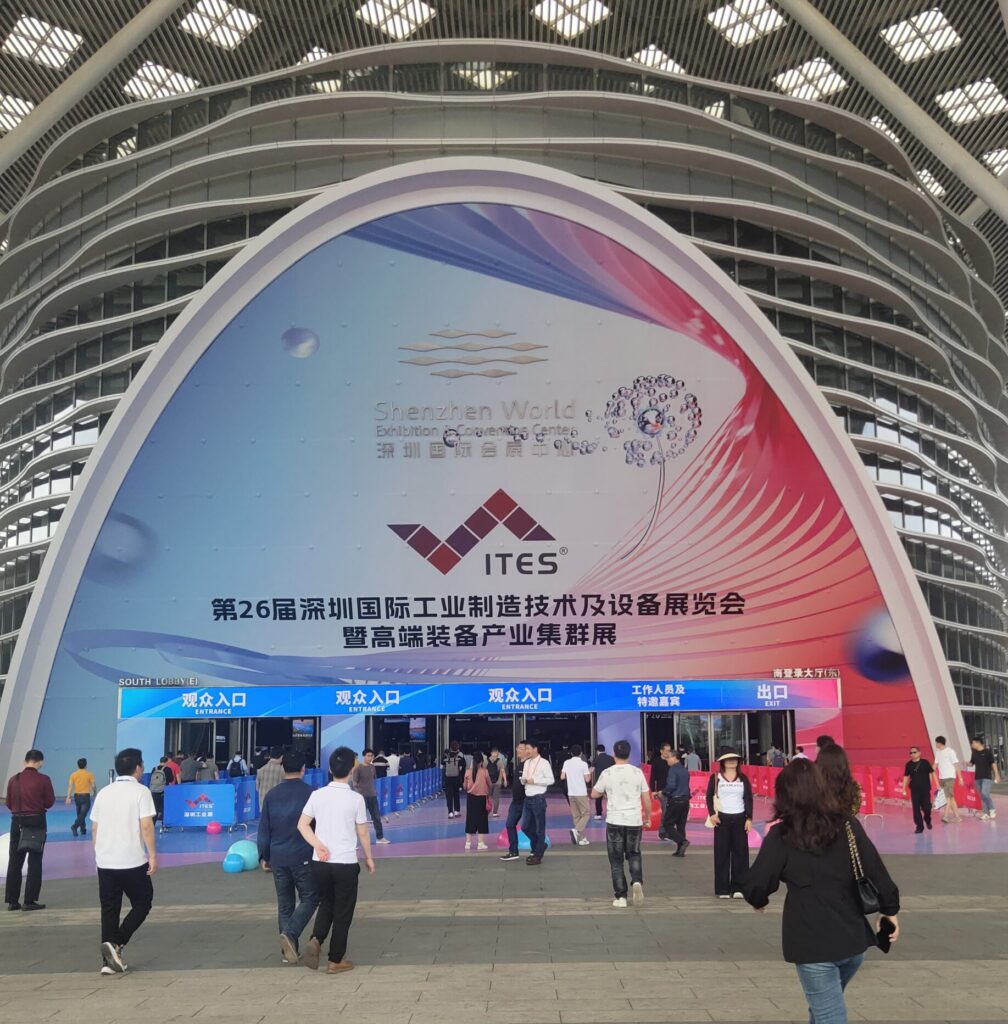
We are keenly focused on advancements in laser equipment and industrial cleaning technologies. Surprisingly, the number of exhibitors specializing in these areas was less than expected. While the limited presence of industrial cleaning equipment manufacturers can be understood, the significance of laser technology in the industry raises questions, especially given the entire afternoon dedicated to discussions on laser advancements.
The afternoon conference featured an impressive lineup of presentations, showcasing pioneering research and practical applications of laser technology:
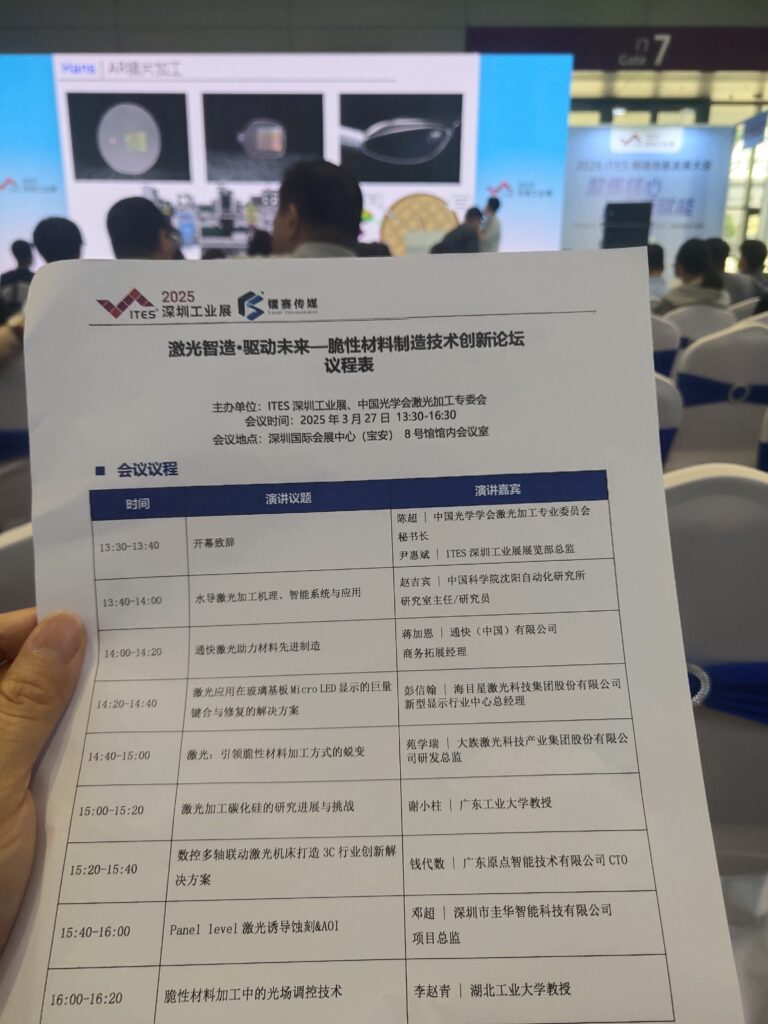
– **14:00-14:20** – TRUMPF Lasers: Catalyzing Advanced Manufacturing in Materials
– **14:20-14:40** – Solutions for Mass Bonding and Repair of Glass Substrates in Micro LED Display Applications Using Lasers
– **14:40-15:00** – Transformative Approaches in Processing Brittle Materials with Laser Technology
– **15:00-15:20** – Progress and Challenges in Laser Processing of Silicon Carbide
– **15:20-15:40** – CNC Multi-Axis Laser Machine Tools: Innovating Solutions for the 3C Industry
– **15:40-16:00** – Panel Level Laser-Induced Etching & AOI
– **16:00-16:20** – Light Field Control Technologies in the Processing of Brittle Materials
One of the most surprising discoveries was a meeting with a local precision grinding manufacturer boasting nearly 60 years of history. The interaction proved to be highly enjoyable, fostering hopes for a successful collaboration in the near future.
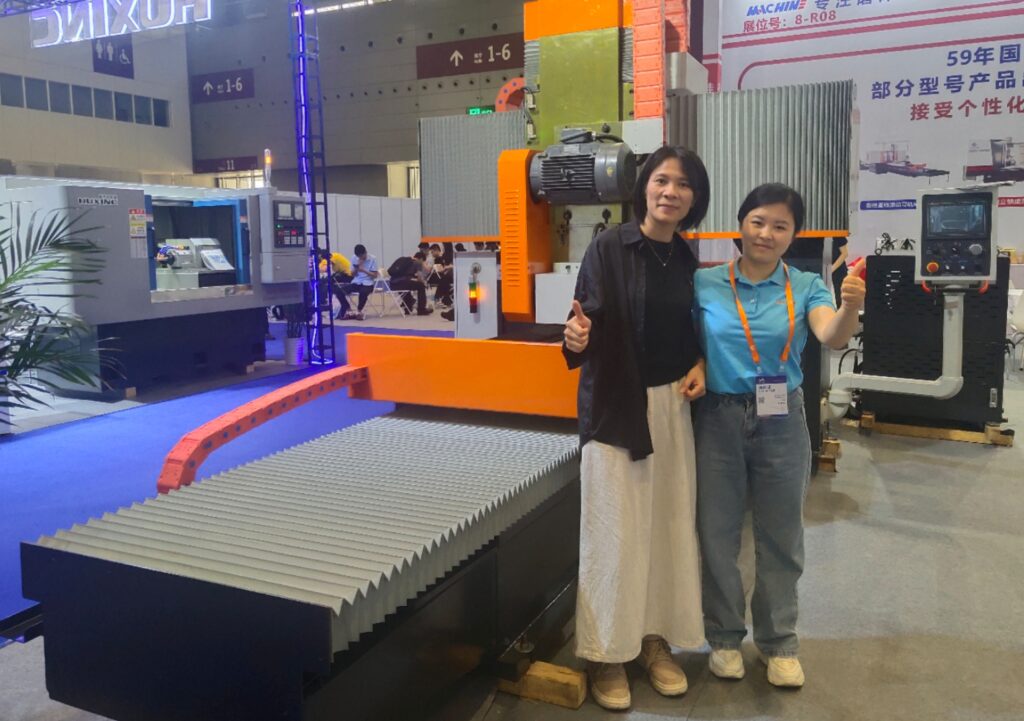
As the exhibition unfolds, industry experts and enthusiasts are eager to explore the latest innovations and potential partnerships, making ITES China 2025 a critical platform for advancing industrial manufacturing technology.
For more updates and details on the exhibition, please visit ITES Exhibition | International Industrial Exhibition 2025 | ITES 2025 (iteschina.com).